Limax Technology
Precision Built In – The Limax Spray System
In electrostatic oiling systems, achieving a uniform spray pattern across the full width of the strip is a known challenge.
With conventional spray bars that rely on spray reservoirs, the spray gap must be manually adjusted along the entire width – a time-consuming and error-prone process, especially after maintenance. Even slight variations can lead to inconsistent results.
At Limax, we’ve developed a unique solution: our spray system uses a high-precision plastic spray bar with an integrated segmented oil distribution plate.
This plate has a fixed and uniform thickness, which means the spray gap is always perfectly set – with no manual adjustment required. The result is:
- Consistently uniform oil mist distribution
- Maximum repeatability – even after servicing
- Significant time savings during setup and maintenance
This is precision by design – and a clear technological advantage for every production line.
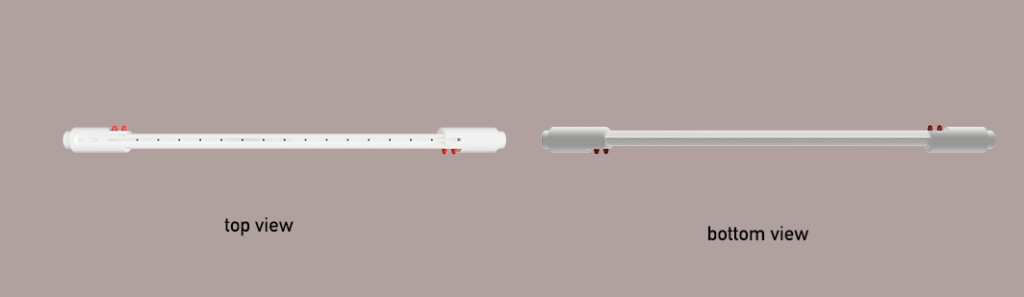
Secondary Electrodes – Finer Mist Through Smart Charge Control
In an electrostatic spray bar, oil is electrostatically charged as it enters the spray gap. After spraying, the natural voltage gradient within each droplet causes the droplet to break apart, forming the fine oil mist essential for uniform coating.
With our unique technology, we take this principle a step further:
By placing a secondary electrode directly after the spray gap, we artificially manipulate the voltage gradient at the critical moment.
This causes the droplets to break earlier and more evenly, resulting in:
- A finer and more consistent oil mist
- Improved surface coverage
- A visibly more homogeneous oil film
This added layer of control ensures a more stable and efficient application process – and sets our system apart from conventional electrostatic oilers.
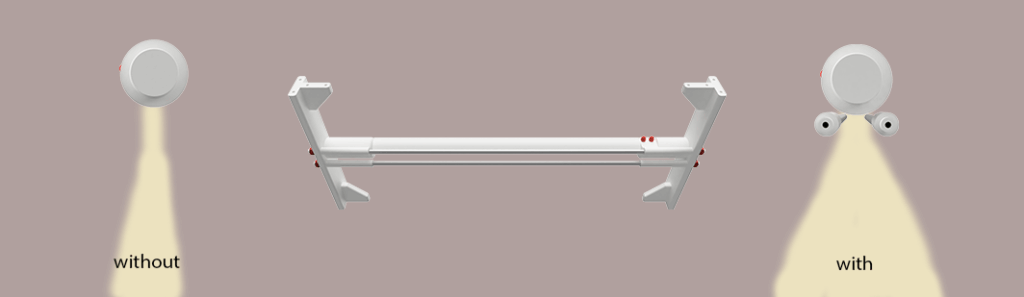
Spray Width Adjustment – Intelligent Control, Zero Waste
Traditional systems often rely on mechanical shielding or time-consuming manual adjustments to control spray width. At Limax, we’ve engineered a smarter solution.
Our spray bar features internal segmentation, allowing the spray width to be adjusted digitally and with pinpoint accuracy. Each segment can be individually controlled via the central software – enabling:
- Precise oil application only where needed
- Significant savings on oil consumption
- Faster changeovers and fewer setup errors
This intelligent width control is not just efficient – it’s sustainable.
By oiling only the necessary areas, we help reduce waste and improve overall process quality.
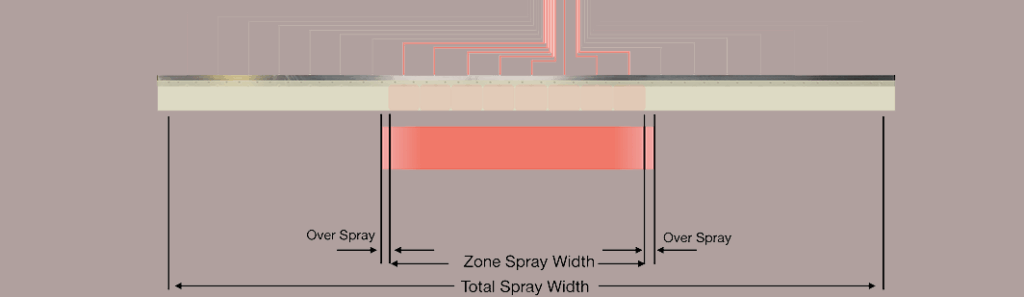
Roll Deflection Compensation – Uniform Pressure, Superior Results
During homogenization, rollers are pressed against the strip to evenly distribute the applied oil.
However, this pressure can cause roller deflection, which in turn affects the uniformity of the oil film across the full width.
With Limax, that problem is solved.
Thanks to our innovative roller design and advanced material selection, we achieve a consistent contact pressureacross the entire roller width – with a deviation of only 2–3%, regardless of the applied load.
The result:
- Perfectly even homogenization
- Improved coating quality
- Reduced roller wear and longer service life
Limax roll technology sets a new benchmark in precision and durability.
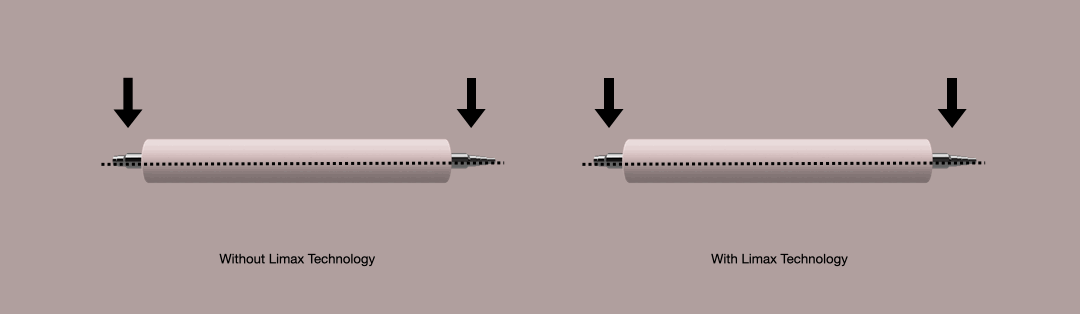
And So Much More.
Curious how our differential dosing enables both ultra-low and high-volume flow rates – using the same pump technology?
Wondering why all our tanks are Hotmelt-ready by default?
Want to know how our re-oiling function in the spray bar targets dry strip zones with precision?
Or how our global service network ensures fast support, wherever you are?
Better yet – do you have challenges with your current electrostatic oiling system?
Let’s talk.
We’re ready to dive in with you – and excited to show what Limax technology can do.
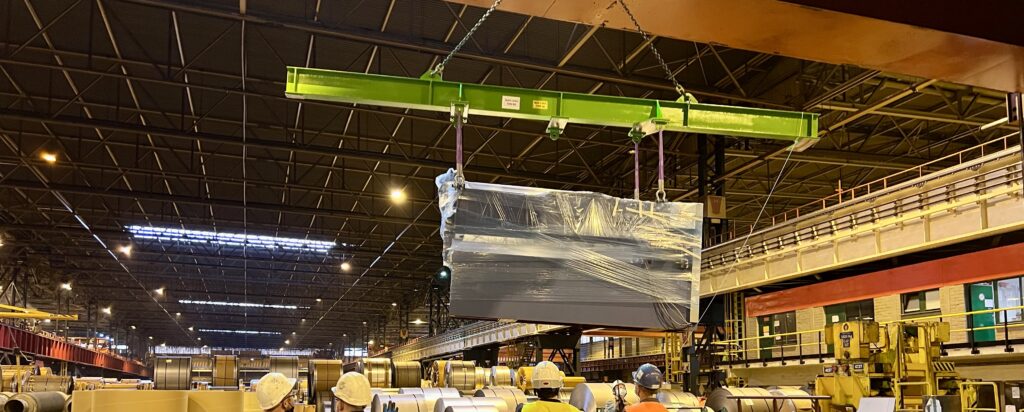